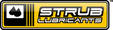
Contact Details:
Strub-SA cc
14/16 Spence Str
Duncanville Ext 3
Vereeniging
Gauteng
1939
South Africa
Tel: +27 (0)16 454 0000
Fax: +27 (0)16 423 1803
Send Enquiry | Company Information
Grease
Product News Thursday, August 27, 2009: Strub-SA cc
WHAT IS GREASE?
Grease is a semifluid mixture of a fluid lubricant (base oil) and a thickening agent (thickner). This combination creates a gel or gel like substance know as grease. The thickening agent can be viewed as a "sponge" that keeps the oil in place. Thickners can be a soap, an organic or inorganic thickner. The "thickness" of a grease is know as the penetration, the NLGI (National Lubricating Grease Institute) has various standards and guides as to what specifications a grease must comply with. Greases are subject to a numbering scale, a 000 being almost fluid like and 00 and 0 semi fluids, the higher the number, the "harder" the grease. For general and in fact about 90% of all applications a NLGI number 2 grease is used. The NLGI numbering scale ranges from a 000 up to a number 6 grease being a solid lubricant. Various additives are added to give the grease certain desired characteristics e.g. high load or high heat resistance. The function of grease is to stay in place or in contact with the moving surfaces and not be squeezed or leak out. Grease is used as a lubricant instead of oil when:
- The lubricant must act as a seal to prevent entry of contaminants.
- The lubricant must maintain its position in the mechanism, in other words, not run out.
Because most greases are semi fluid to solid in nature they do not have the same cooling and cleaning capability of fluid lubricants but except for these, grease performs all of the other functions of oil. Grease for a given application must:
- REDUCE FRICTION and WEAR.
- Protect against rust and corrosion.
- Prevent dirt, water and other contaminents.
- Resist leakage.
- Maintain its structure.
- Permit free motion at low temperatures.
- Be compatible with the seals of the equipment being lubricated.
THE CHOICE OF GREASE.
Having to choose a grease product for a particular application can be a difficult task, however a few simple questions can help you make the correct choice:
- What is the maximum operating temperature?
- What is the maximum operating speed?
- Will there be moisture involved?
- Can the equipment be re-lubricated on a regular basis?
- Remember that the re-lubrication period is very important because certain equipment will only be lubricated once for their entire life e.g. a DIY electric drill. So we can see taking the time to consider all of the above will greatly assist you in making the correct choice in grease.
PENETRATION OF GREASE.
When referring to the penetration of grease, we are referring to the consistency or hardness of grease. The NLGI has a numbering scale for different grades of grease, this scale ranges from 000 to 6, with 000 being fluid like and a number 6 very hard or solid. The penetration of a grease is very important because different applications require different grease consistencies, otherwise leakage, clogging and overheating of the grease and equipment could occur. In almost 90% of all applications a number 2 grease is used. When selecting a grease, the penetration is also very important because in many applications the re-lubrication is done by pump, therefore the pumpability of the grease is crucial in this type of application. The harder the grease, the more strain on the pump delivering the grease to the moving parts. Always keep in mind how the grease will be applied to the work zone.
On looking at a datasheet of a grease product the "Worked Penetration" may be given as a specification, what is Worked Penetration you may ask? To measure the Worked Penetration of grease, a container with grease is worked with a piston like plunger for a set amount of strokes, normally 60, then the penetration is measured again. This test gives us an indication of how soft the grease will go while in use, this is crucial as with fluid lubricants a grease also has to "stay in grade" and not fall out of specification.
OTHER TESTS AND CONSIDERATIONS WHEN SELECTING A GREASE.
Various other tests and specifications may be considered when choosing a grease for an application. Grease Shear Stability, Dropping Point and the Extreme Pressure (Four Ball Test) may be considered.
Grease Shear Stability.
The Shear Stability of a grease or mechanical stability is the ability of the grease to withstand repeated working with minimum change in its structure or consistency.
Dropping Point.
The Dropping Point of grease is that temperature at which grease passes from a semi-solid to a liquid state. It is crucial to know this temperature because in applications requiring a semi-solid grease, a grease that has gone too soft wont give adequate lubrication.
Extreme Pressure (Four Ball Test).
To test how a grease handles Extreme Pressure a test known as the Four Ball test is done. Four steel balls are placed in a tetrahedron form (three balls at the bottom in a triangular shape with one ball on top) inside what is known as a four ball testing device. The four balls are submerged in grease, the ball at the top is rotated at about 1800rpm while resting on the other three balls. A series of 10-second runs are made at different loads until welding of the four balls occur. Measurements are then made of the load scars on the balls and an average diameter is taken of the weld points (scars). This measurement is then used in calculations to determine the Extreme Pressure value.