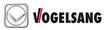
Contact Details:
Vogelsang
7966 State Route 44
Ravenna
OH
44266
United States of America
Tel: +01 330 510-1558
Alt. Tel: +01 800 984-9400
Fax: +01 330 296-3820
Send Enquiry | Company Information
Why an Engineer would specify a Rotary Lobe Pump
Product News Monday, February 11, 2013: Vogelsang
The rotary lobe pump has become a leading example of modern positive displacement pump design. Exciting new innovations and developments are being introduced each year. Based on the Blower principle, the concept has evolved over decades from a niche product to one of the fastest growing products for pumping applications. As the design continues to evolve, new applications are constantly discovered.
But why would an engineer switch from an industry standard to something new? Especially if a customer is expecting a certain product, it would naturally be specified, right? Discovering the advantages of the rotary lobe pump can create previously unknown cost savings in many aspects of the design process. Savings can be found in areas such as simplifying a process to reducing the size of a building. Savings can also be found in reduced operation and maintenance costs. An engineer who recommends a rotary lobe pump can reduce the customer’s expense in both the immediate and the long term.
Below are two sections presenting the attributes of the pump in terms of its physical construction and design followed by how it performs under various operating scenarios.
PHYSICAL CHARACTERISTICS
Maintenance
Rotary lobe pumps are considered low maintenance compared to other positive displacement pumps. Brands vary in complexity of the wet end design. Some brands are simple using only a minimum of wear parts including, one-piece rotors, robust cartridge seals, heavy-duty bearings and solid shafts without step-downs. Several brands feature an easy access front cover allowing complete access to the wet end of the pump. Brands featuring a quick access cover can typically be rebuilt in one to two hours depending on the exact model and configuration (fig. 1).
[Fig. 1]

Why this is important:
- Labor: When compared to progressing cavity (PC) pump, the rotary lobe pump can reduce routine wet-end maintenance by up to 90%! The rotary lobe pump is maintained in-place without disconnecting flange piping or physically removing it from the base. On average it can take two or three people eleven hours to perform a complete wet-end rebuild on a 200gpm PC pump. In contrast, a rotary lobe pump of the same capacity can be completely rebuilt by one person in about one hour! Choosing a rotary lobe pump can drastically reduce the customer’s maintenance budget.
- Expense: When compared to a PC pump, the rotary lobe pump is inexpensive to maintain. It’s often possible to install a new rotary lobe pump for the cost to fully rebuild a PC pump – which would include replacing the rotor, stator and mechanical seal. Parts cost vary by brand and model plus, there are a lot more aftermarket sources for PC pump replacement parts. Due to the nature of how both pumps operate, the PC pump often requires immediate service for high wear or run-dry situations. In contrast, the rotary lobe pump can simply be sped up to maintain flow, allowing maintenance to be done at the customer’s leisure.
Size
The nature of the design makes a rotary lobe pump more compact than some other positive displacement pumps. Rotary lobe pumps pack the high capacity into a small package. Being that the bare pump is smaller than most other positive displacement pumps, additional space savings can be realized by attention to the assembly type. Most brands offer the traditional straight-coupled assembly consisting of the pump, C-faced motor with gearbox and a sure-flex style coupling. However, for installations where space savings is a concern, most brands offer a V-belt driven ‘piggy-back’ assembly where the motor sits on a top-mounted frame above the pump. This is a highly compact footprint and uses precious space effectively.
Why this is important:
- Building Costs: PC pumps are, on average, 50% larger than rotary lobe pumps of the same capacity (fig.2). For design/build projects, the extreme space savings that the rotary lobe pump provides can be used to reduce the overall size of the building. This not only translates to reduced building costs, but also affects maintenance and utility costs.
- Maintenance: PC pumps also require at least one full rotor-length in front of the pump in order to service the wet-end (fig. 2). Additionally, for larger capacity pumps, a crane or other lifting device is required to effectively handle the stator. In contrast, a rotary lobe pump only needs a reasonable area for a person to work in front of the pump. There are many large rotary lobe pumps on the market where a single lobe may weigh over 100lbs., but typical applications will call for a pump with lobes weighing around 20-40lbs. apiece.
[Fig. 2]
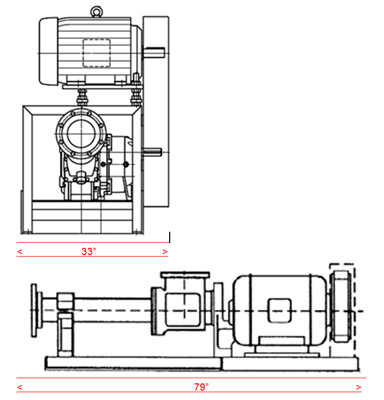
Power Requirements
Rotary lobe pumps make very effective use of electricity. As a group, they are typically equally efficient or better than other designs. Rotary lobe pumps vary by brand in terms of the flow rate to horsepower so it is important to look at motor in which is being offered for an application.
Why this is important:
- Air Operated Diaphragm Pumps (AOD): When comparing an AOD pump to a rotary lobe pump, the initial acquisition cost heavily favors the AOD in most cases. However, it is often overlooked that the AOD consumes a lot of energy to operate the compressor. As a comparison, a 100gpm running at 40psi AOD pump requires around 80cfm of air - which translates to about 21hp. A rotary lobe pump operating under the same conditions only requires 5hp. This translates into increased long-term operating costs to the customer.
- PC Pumps: Rotary lobe pumps and PC pumps use about the same amount of power to operate. However, the PC requires more starting torque to get the flow moving. A larger motor is often required which can affect acquisition cost on larger projects.
PERFORMANCE CHARACTERISTICS
How a rotary lobe pump works
The rotary lobe pump is part of the positive displacement group. It works from the same principle as all positive displacement pumps in that it creates flow by trapping liquid from the suction side, carrying it through the pump and expelling it out the discharge side. What makes the rotary lobe pump special is how it accomplishes this. During operation, two rotors mesh together and rotate in opposite directions (fig. 3). The rotation forms cavities between the rotors and wet-end housing. The liquid that fills the cavities is carried through the pump and expelled out the discharge side.
[Fig. 3]
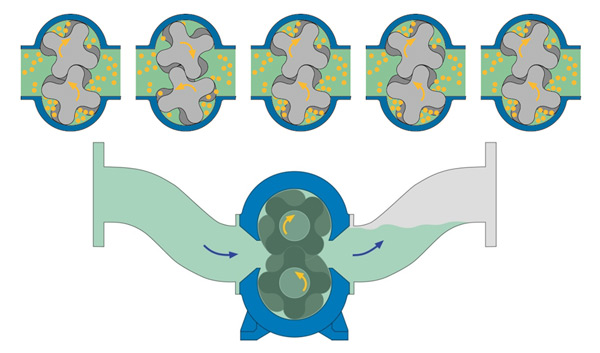
Effects of Slip & High Viscosity
The rotary lobe pump is designed to operate with a controlled amount of slip. Slip, in relation to a rotary lobe pump, is a slight backflow of liquid across the front and back of the wet end and over the tips of the rotors caused by the discharge pressure (fig. 4). The slip is present because the rotors do not actually touch each other nor do they touch the pump housing. The clearance between the lobes and the housing is small at around 1mm. This clearance requires precise timing of the wet end components. Some rotary lobe pump designs use complex timing gears to achieve this. It is recommended to specify a brand that uses keyed shafts which are preset and do not require timing.
[Fig. 4]
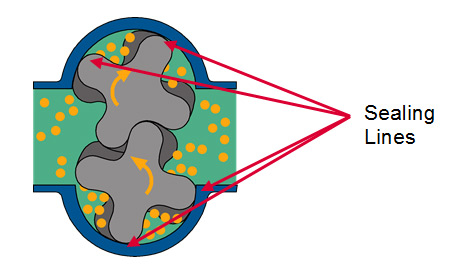
Why this is important: Slip is actually advantageous for three reasons.
- Where there is no contact, there is no friction. The absence of friction between moving parts allow the pump to run dry. On typical self-priming suction-lift applications, it is advantageous to choose a pump that can run dry indefinitely. PC pump and many gear pump users struggle with run dry in application where the pump may run dry. It is widely known that rotary lobe pumps can self-prime and run dry. However, not all brands are clear about their run-dry capability so it is recommended to choose a brand that offers specifics about their product.
- Where there is no friction, there is no restriction on materials of construction. The lack of contact also means that rotary lobe pumps can be installed with high wear materials that would not be suitable to come into direct contact. Applications involving liquids containing grit, abrasives or caustic elements demand high wear wet end materials. Pumps relying on direct contact between wet end elements, such as PC pumps, can experience increased wear in certain applications. Rotary lobe pumps can choose from a variety of elastomer coatings over the rotors or even use stainless steel, tungsten carbide or ceramic coatings.
- Rotary lobe pumps become more efficient as the viscosity of the liquid increases whereas centrifugal pumps become less efficient. As the viscosity increases, the slip reduces to the point that it is negligible. Slip only becomes an issue in applications better suited for a centrifugal pump.
Example Applications
- Abrasives & Chemicals: Pigment, Ink, Fiberglass Resin, Dustac, Alumina Slurry
- Heavy Viscous Sludge: Belt Press Sludge Feed, Centrifuge Feed, Plate & Frame Press Feed, Rotary Press Feed, Settled Solids, Drilling Mud, Paper Sludge, DAFT Sludge, Kaolin Clay
Hard Solids Handling
Due to the nature of the operating principle, solids handling comes naturally for a rotary lobe pump. Any hard solid that can fit in the rotor cavity can be passed through the pump. The maximum size of the hard solid is determined by the size of the pump housing and the design of the rotor. The larger the overall size of the pump allows for larger solids handling. Lobe design is important when dealing with hard solid objects. Pumps using a straight two-lobe rotor can pass the largest solid simply because it creates the largest cavity. However the two-lobe rotor is also the least efficient in terms of pumping performance. A compromise must be made to determine the most effective way to handle solids if high efficiency flow is also required.
Why this is important: Applications dealing with large objects in the liquid are well suited for a rotary lobe pump. There are many rotor designs to choose from that will allow a large solid to pass and still deliver the required flow and pressure.
Reversible Flow
As the rotors spin inside the wet-end housing (as shown in fig. 3), a steady flow is created. The direction of flow is set by the rotation of the lobes. Looking at the wet end of the pump, the top lobe is spinning clockwise, which causes the bottom lobe to spin counter clockwise. This results in a left-to-right flow. If the top lobe reversed to counter clockwise, making the bottom lobe spin clockwise, the flow would reverse to a right-to-left flow.
Why this is important: There are many applications where it is desirable to have a pump capable of reversible flow. Perhaps the customer needs to back flush a line, empty a tank or clean a membrane. If they are using a centrifugal, PC or air operated diaphragm pump, they must use secondary valves and piping to achieve a reverse flow. A rotary lobe pump can reverse on the fly at any time and the capacity and efficiency are the same in either direction.
Example Applications: Tank cleaning, tank and line stripping, MBR permeate, back flushing, oil offloading & loading.
Pulsation Free Flow
Rotary lobe pumps can produce a pulsation-free flow of liquid provided that they use a convoluted style rotor with at least 4 lobes per rotor (fig. 6). Not all brands offer this so it is important to become familiar with the rotor style of the brand under consideration if pulsation is a factor in the application. Some brands even use dampener devices to mask the high pulsation causes by straight two and three lobe rotors. Brands offering convoluted style rotors with 4 and 6 lobes per rotor can provide pulsation free flow of liquid in either direction.
[Fig. 6]
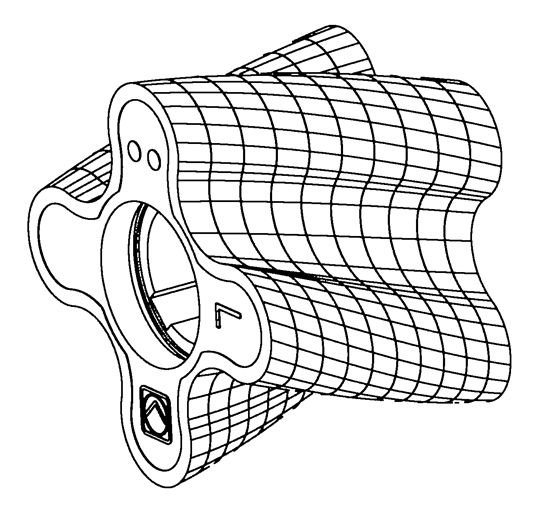
Why this is important: There are many applications where pulsation can affect the performance of downstream process equipment. Applications involving accurate dosing or metering will benefit by eliminating pulsation. Pulsation can also affect infrastructure such as valves and piping. A smooth and even flow of liquid allows an entire system to perform efficiently.
Example Applications: Belt Press Sludge Feed, Centrifuge Feed, Plate & Frame Press Feed, Rotary Press Feed, Metering, Dosing, On & Offloading.
Shear Free Flow
The discharge pressure of a rotary lobe pump is not dependent on the RPM of the rotors. Unlike a centrifugal pump, the rotary lobe pump can produce a required discharge pressure even at low flows. As a result, the rotary lobe does not shear the liquid or entrain air.
Why this is important: There are many applications where shearing has adverse affects on the liquid. If the liquid is a product, versus waste or byproduct, it is desirable to affect it as little as possible. Even with waste liquids, shearing can adversely affect downstream process devices.
Example Applications: Food & Beverage processing, Wineries, Sugar & Molasses Process, Chemicals, Oil & Gas.